​
Annual Applied Science and Engineering Conference (AASEC) 2019
TYPE
Research Paper
​
AUTHORS
Mia Rismalia
Samuel Christian Hidajat
I Gede Raditya Permana
Farid Triawan Dr. Eng
​
DATE
Oct 2018 - April 2019
​
TOOLS
Abaqus, SolidWorks, Cura, Word, Exce
OVERVIEW
​
- Researched and did a literature review to discover possible uses of origami structures.
- Created an Origami-Inspired structure for energy absorber applications.
- Analyzed the performance of the energy absorber using FEA software.
- Conducted experiments utilizing 3D printers and universal testing machine based on ASTM standards to validate the FEA results
Those 3 (three) research are entitled as:
1. “Study on the Infill Pattern and Density Effect on the Tensile Properties of 3D Printed PLA Material.”
2. “Finite Element Analysis of Miura Origami Structure under Uniaxial Compressive Load.”
3. “Study on the Compressive Behavior of Miura-Origami Lattice Structure.”
​

In this work, an investigation of the relationship between two printing parameters, i.e. infill pattern, and infill density were conducted on the Polylactic Acid (PLA) material. Three infill densities, 25%, 50%, and 75%, and three infill patterns, grid, tri-hexagon, and concentric, were chosen. The tensile test, ASTM D638, was employed to obtain the material properties based on these two printing parameters. An open-source 3D printing slicer software, Cura, was used to manufacture the tensile specimens. The Young's modulus, yield strength, and ultimate strength were recorded and examined.
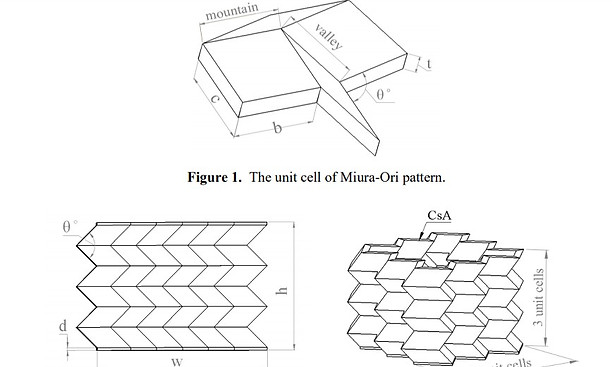
In this paper, the compressive behavior of 3D printed column structure using the Miura-origami pattern is investigated. Polylactic Acid (PLA) material was used to make the specimen with various printing parameters, i.e. infill pattern and density. Moreover, six kinds of origami patterns with different folding angles and wall thicknesses were tested. Finally, the elastic and plastic deformation behavior under compressive load is examined. In addition, this study is expected to give an impact on developing an innovative engineering design by the use of the Miura-Ori pattern.

This paper presents the finite element analysis (FEA) of 3D printed Miura origami column under uniaxial compressive loading condition. The finite element model (FEM) was developed under the elastic-perfectly plastic material model. Investigation on the yield strength and compressive modulus with two varied parameters, i.e. angle and thickness of the Miura origami column was conducted. Abaqus 6.14 software was used to conduct the simulation of the compression test. The simulation result is then compared with and examined to the referred experimental data.
REFLECTION
​
Key Learning
​
1. Develop my collaboration and time management skill to finish the project on time.
2. Communication skills really needed at that time due to making a report and presentation.
​
​
PEER- REVIEW
​
"Mia is an individual with high drive and constant optimism. When we were working on a team project and encountered roadblocks she was able to face the situation with a positive attitude without losing sight of the end goal, driving positive energy to the team. She always finds a way to deal with challenges and in result, completes her tasks with flying colors."
​
- Samuel Christian Hidajat, Management Associate - IT Architecture & Digital Development at Bank OCBC NISP.
​
​